Eddy current testing (ECT) is a great non-destructive testing (NDT) method. It’s essential for the safety and reliability of aerospace, automotive, and manufacturing components.
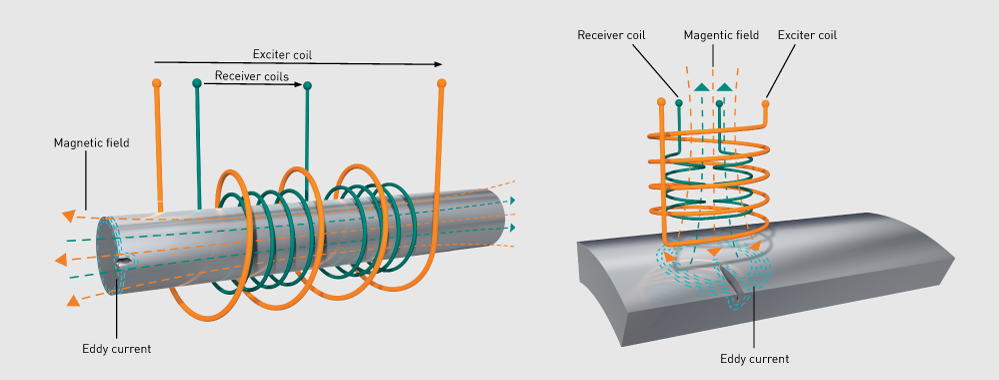
Table of Contents
So, what is ECT? It’s a technique that uses electromagnetic fields. It detects flaws in conductive materials without damaging them. Imagine being able to inspect a metal part without having to cut it open – that’s the benefit of ECT!
Here’s how it works:
An alternating current flows through a coil. This creates a changing magnetic field. When this coil is placed near a conductive material, it induces eddy currents in the material. Any flaws, like cracks or corrosion, will disrupt the eddy currents. The testing equipment can detect that disruption.
ECT is used in many applications. In aerospace it’s used to inspect critical components like wings and fuselage. In automotive it’s used to inspect engine parts and assemblies. Manufacturing industries use it for quality control and safety standards.
The benefits of ECT are many: it’s fast, highly sensitive to small flaws and can be done on-site which saves time and cost. And because it’s non-destructive you can inspect multiple times over the life of a component.
But ECT has its limitations. It only works on conductive materials so not suitable for non-metallic materials. It can be affected by surface conditions. A skilled technician must interpret the results.
Eddy Current Testing Principles
Electromagnetic Induction
Eddy current testing relies on a simple principle: electromagnetic induction, from Faraday’s Law. A changing magnetic field generates an electric current in a conductive material. This current doesn’t just flow straight; instead it forms loops called eddy currents. We can measure and analyze these currents. It will show us the material’s integrity.
Eddy Current Formation
Eddy currents are formed when a conductive material encounters an alternating magnetic field. Several factors affect how strong and where they are:
Material Properties: Different metals exhibit unique behaviors. For example, copper and aluminum produce strong eddy currents. Less conductive alloys produce weaker ones.
Frequency: The frequency of the alternating current is important. Higher frequencies produce shallower currents good for surface defects.
Geometry: The flow of the eddy currents also depends on the shape and size of the material being tested. A larger or oddly shaped object will create a different current pattern than a small, uniform one.
Eddy Currents in Material
Once eddy currents flow through a material, they interact with it in interesting ways. As they flow they can change the material’s impedance and phase. Lenz’s Law tells us that these currents create opposing magnetic fields. They oppose the original change in the magnetic field. This is key for detecting defects. Cracks or corrosion will disrupt the flow of the eddy currents. This disruption signals that something is wrong. We can find potential problems before they grow into big issues.
Eddy Current Equipment: Tools for Accurate Testing
The accuracy of Eddy Current Testing relies on specialized Eddy Current Equipment, which includes a range of devices that help to create, measure, and analyze the eddy currents. These tools are customized to suit specific testing tasks.
1. Eddy Current Flaw Detectors
- Purpose: These devices are used to detect surface and near-surface defects in metallic components.
- Features: They often feature digital displays, multiple frequency settings, and sensitivity adjustments to allow technicians to fine-tune the equipment for different materials and defect types.
- Applications: Used in industries like aerospace to inspect aircraft components such as turbine blades and fuselages, and in automotive to inspect engine components and brake rotors for cracks.
2. Eddy Current Probes/Sensors
- Purpose: Probes are the direct interface between the testing equipment and the material being tested. These sensors generate the eddy currents in the material and detect any disruptions caused by defects.
- Types of Probes:
- Encircling Coils: Used for measuring the entire circumference of cylindrical objects like tubes or rods.
- Surface Probes: Used for inspecting flat surfaces or accessing hard-to-reach areas.
- Rotating Probes: These are ideal for inspecting curved surfaces or complex geometries, especially in semi-finished products like wires and tubes.
- Applications: Probes are used in testing applications across a wide range of industries, including energy (to inspect heat exchanger tubes) and railways (to detect flaws in tracks).
3. Eddy Current Thickness Gauges
- Purpose: Eddy Current Thickness Gauges are handheld devices that measure the thickness of non-ferrous materials, coatings, and metal components.
- Features: They provide fast, non-destructive measurements and can be used directly on-site without the need for extensive setup.
- Applications: Commonly used in manufacturing to check coating thickness on metal parts and to assess the wall thickness of pipes in the oil and gas industry.
4. Eddy Current Conductivity Meters
- Purpose: These meters measure the conductivity of materials, which can indicate their composition or whether they have undergone a heat treatment process.
- Features: These handheld devices are essential for material sorting and identification, providing a quick assessment of a material’s properties.
- Applications: Conductivity meters are often used in quality control during metal sorting in manufacturing processes, particularly in industries such as automotive and metallurgy.
5. Eddy Current System Software
- Purpose: Software platforms are used to analyze the data collected from the equipment. They process complex signals and offer advanced visualizations, making it easier for technicians to interpret test results.
- Features: These systems allow users to store data, generate reports, and track defects over time. Some systems even have the capability for automated defect detection.
- Applications: Often used in high-volume manufacturing environments, where detailed inspection data is needed for ongoing quality control.
Eddy current methods in semi-finished product and component testing
Eddy current testing for semi-finished product and component testing covers a frequency range up to 10 MHz and is used to detect surface defects in metals. Many different differential coils are used for this. Standard sensors as well as custom adaptations.
Semi-finished products like wires, rods and tubes are tested for transverse cracks and hole-like defects with the encircling coils, the surface of semi-finished products are tested for longitudinal defects with rotating probes.
Stationary probes can also be used to test critical points on components. The right sensor always depends on the testing task. This allows for very high defect resolution.
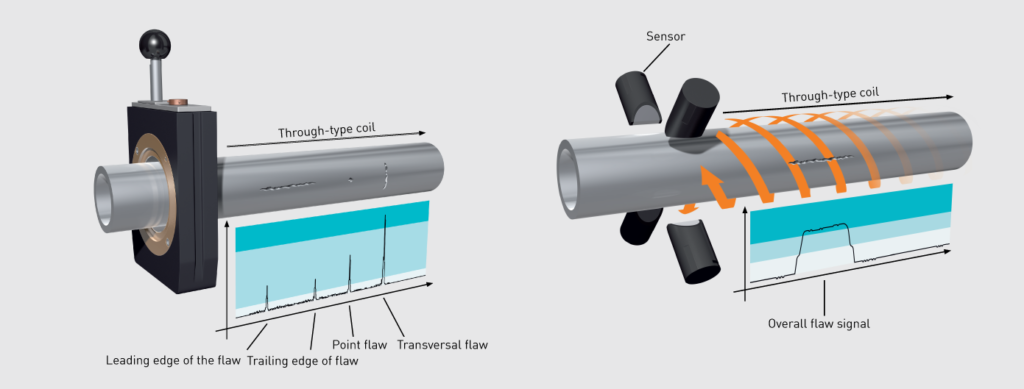
Image source: Foerstergroup.com
Eddy Current Testing Applications
Aerospace
In the aerospace industry ECT is used to ensure the safety of aircraft. It’s used to inspect fuselages and wings for cracks or corrosion that could be catastrophic. Regular inspections prevent failures and keep planes safe.
Automotive
The automotive industry uses ECT for safety parts, like brakes and suspension. ECT detects cracks in brake rotors early. This ensures vehicles are safe and reliable for drivers and passengers. It’s all about keeping the roads safer!
Energy
Power plants use ECT to test heat exchanger tubes. They can corrode due to high temperatures and pressures. Regular inspections with ECT ensure efficiency and safety. They keep these critical systems running smoothly.
Manufacturing and Quality Control
Manufacturers use eddy current testing in quality control. It detects surface defects in metal parts. This approach ensures high quality. It reduces failure. So, it leads to better products and happier customers.
Other Industries
ECT isn’t limited to those industries; it has applications in many others. In railways it’s used to detect flaws in tracks so trains can travel safely. In the marine industry, it’s used to inspect ship hulls for corrosion so vessels don’t get damaged. It can also be used to test the hardness of metal components, so it’s not just versatile but also multi-talented.
Eddy Current Testing Advantages
Non-Destructive
One of the biggest advantages of eddy current testing (ECT) is it’s non-destructive. The tested component must remain unharmed. This is critical in high-risk industries where any damage is unacceptable. You can inspect critical parts without worrying about compromising them.
Speed and Efficiency
ECT is fast, so it’s great for high-volume inspection environments like manufacturing. When speed is key, inspecting many parts without losing quality is a big advantage.
Surface and Near-Surface Defects
Eddy current testing is good at detecting surface and near-surface defects. So, we can detect cracks or corrosion early. This allows for maintenance to prevent bigger problems later.
Universal
Another advantage of ECT is it’s universal. You can use it on all conductive materials, including steel and aluminum. So it’s a valuable tool in many industries.
Eddy Current Testing Limitations
Material Restrictions
ECT is great for conductive materials. But, it doesn’t work on non-conductive ones like plastics or ceramics. So you need to consider the materials involved.
Surface Preparation Requirements
To get accurate results, testers must ensure that the surfaces are clean and smooth. This often requires some prep work, which can add to project timelines. A little extra effort goes a long way in getting reliable testing.
Depth of Penetration Challenges
Eddy current testing is good for surface and near-surface defects. But it is less effective on thick materials. For deeper defects, you may need other tests. So know the limits when assessing a component.
Skill and Training Requirements
Interpreting the results of ECT is not simple; it requires skilled personnel. Operators need training to understand signal analysis. This can be a barrier for some companies. Invest in this training to get the most out of ECT.
So there you have it! Eddy current testing has many advantages but also has limitations. Now balance them out!
Conclusion
Eddy current testing (ECT) is a non-destructive testing (NDT) tool. It is used across many industries. ECT uses electromagnetic induction to detect surface and near-surface defects. It does so without damaging the tested material.
It has limitations. It only works on conductive materials and needs clean surfaces. But, its speed, sensitivity, and versatility make it a popular choice for many uses. As industries focus on safety and quality, eddy current testing will be vital. It will ensure our components and systems are reliable and safe.
Frequently Asked Questions
What is eddy current testing?
ECT is a non-destructive test. It uses electromagnetic induction to find defects in conductive materials.
How is eddy current testing done?
The process involves setting up equipment, conducting tests, and analyzing data for variations indicating defects.
How much does eddy current testing cost?
Costs vary depending on the application, material, and scope of testing.
How often should eddy current testing be performed?
The frequency depends on industry standards, component criticality, and regulatory requirements.
What is eddy current testing used on?
ECT is commonly used on metals, including aluminum and steel, in applications such as crack detection and assessing material integrity.